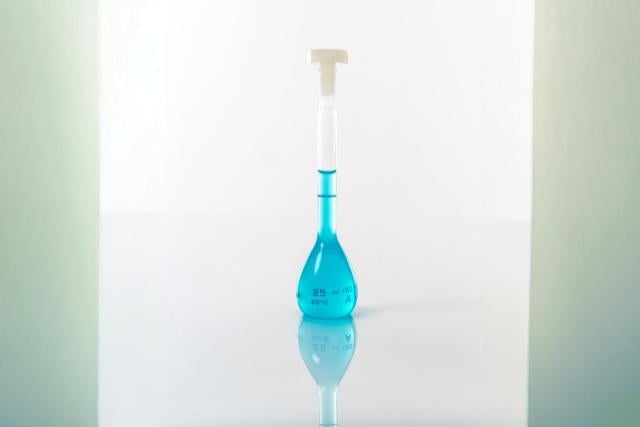
Lithium producers are increasingly recognizing the importance of sustainability as there is increased demand for lithium hydroxide due to the use of electric vehicles (EVs) and renewable energy storage. With environmental concerns arising, investors to customers are prioritizing green activities. To address this, there are some producers of lithium hydroxide that are shifting towards sustainability in operations, especially the greener mode of production, recycling processes, and minimizing carbon footprints.
Environmentally Friendly Production Methods
One of the biggest areas in which companies are adopting greener methods is their production processes. The conventional lithium extraction practices, specifically from hard rock (spodumene) and brines, have faced criticism for posing an enormous ecological impact, i.e., water consumption, energy input, and ecological devastation. Therefore, leading lithium hydroxide players are shifting towards more environmentally friendly processes and streamlining their current practices to minimize environmental footprints.
Albemarle Corporation, being a major producer in the lithium industry, has, for instance, implemented water-conserving techniques in extracting lithium. Albemarle has invested in new processes such as direct lithium extraction (DLE), which consumes significantly less water compared to common brine evaporation processes. This shift to more sustainable practices not only reduces the environmental impact but also enhances the overall efficiency of the production process.
Recycling Programmes for a Circular Economy
Recycling forms the nucleus of improving the sustainability of the lithium hydroxide industry. The majority of companies are embracing recycling processes for lithium from used batteries and other waste materials, which helps in promoting the setting up of a circular economy. This way, they reduce the need for raw materials, lower energy usage, and reduce overall environmental footprint. Livent Corporation, for example, has launched initiatives to recycle lithium from spent electric vehicle batteries and other lithium-ion items. The company has established a patented battery recycling process which recovers high-purity lithium from exhausted batteries and uses it again in the manufacture of new batteries. Tesla, in addition to this, has invested significantly in battery recycling technology. The company's Gigafactories are integrated with battery recycling as part of their manufacturing process. Tesla, for its part, seeks to recycle over 90% of the materials in their EV battery, such as lithium, cobalt, and nickel, cutting down on environmental impacts related to extracting these metals.
Carbon footprint reduction
Another vital component of sustainability in the lithium hydroxide market is carbon emission reduction. Businesses are increasingly endeavouring to minimize their carbon footprints from mining to manufacturing to transportation along the supply chain. SQM (Sociedad Química y Minera de Chile), one of the leading lithium producers, is planning to be carbon neutral by 2040. The company is making a concerted effort to cut greenhouse gas emissions through energy efficiency, the use of renewable energy, and streamlining mining operations to reduce its impact on the local ecosystem. SQM is also exploring technological development that will enable it to produce lithium hydroxide more sustainably, including low-carbon extraction processes and energy-efficient manufacturing processes. Piedmont Lithium, an American developer of lithium, has also prioritized carbon reduction high on its agenda. The company plans to power its lithium extraction operations using clean and renewable energy sources, minimizing the environmental impact of its operations. On top of this, Piedmont is working in partnership with the local government and environmental organizations to ensure that its operations disturb the local wildlife and landscape as little as possible. This continuous development of more sustainable practices allows the companies to align with global efforts toward a greener future while enhancing the overall efficiency of their production processes.
With growing demand for lithium hydroxide on a global level, the responsibility of the industry towards sustainability is becoming bigger by the day. Top lithium hydroxide manufacturers are adopting a range of ecologically sustainable production processes, recycling schemes, and efforts to minimize carbon footprint. These measures not only reduce production and mining of lithium's carbon footprint, but also are part of the larger green movement towards a greener, more sustainable future. The industry of lithium hydroxide is well-positioned to lead the transition away from fossil fuels and towards clean energy and electric vehicles globally through continued innovation and a commitment to sustainability.
Sources:
Research Org: Science Direct
Government Organization: World Climate Foundation