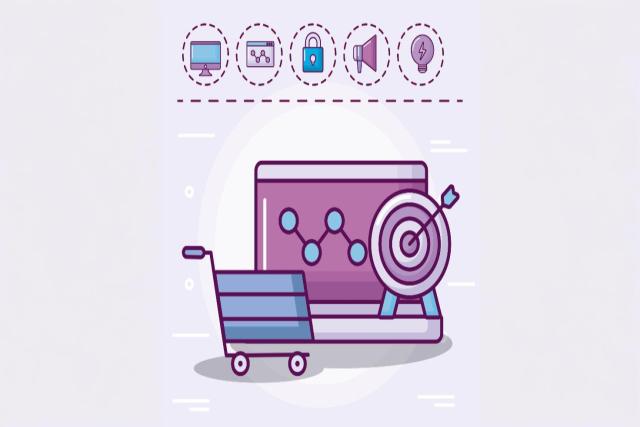
When it comes to ensuring optimal performance, reliability, and long life in industrial environments, it is an important decision to choose the right optical coders. Optical coders are known for their accuracy and the ability to work in different environments, to automate processes, increase the performance of the machine, and reduce the total ownership costs. Choosing the best optical codes for your industrial application requires a deep understanding of your operational requirements, environmental factors, and technical specifications that will be best for your system. In this blog, we will detect factors to consider when choosing an optical code, the type, and what specifications are important for industrial applications.
Why choosing the right optical codes is important
Optical coders are important components of industrial systems where precision and reliability are not negotiable. These codes provide the essential feedback needed to monitor machine movements, location, and speed. When selected correctly, they not only improve the efficiency of the machine but also contribute to the costs of low maintenance by reducing the possibility of errors and downtime. The right optical coder ensures continuous operation by providing precise real-time feedback. This can significantly extend the life of machines at the same time as the total production.
Types of Optical Encoders for Industrial Applications
Optical encoders come in different designs, each serving distinct industrial purposes. When selecting the right encoder, it's important to understand the types available and their applications.
Incremental Optical Encoders: These encoders generate pulses each time the encoder disc rotates. They are widely used in systems that require measuring rotational position or speed, and they’re ideal for applications that don’t need an absolute position after a power cycle. Incremental optical encoders are often used in systems where the position is re-established after each startup.
Absolute Optical Encoders: Unlike incremental encoders, absolute optical encoders provide a unique position for each part of the rotation. They’re designed to retain position data even when power is lost, making them perfect for applications where continuous, precise positioning is necessary. These encoders are typically used in high-precision applications, like robotics and automated manufacturing, where maintaining an accurate position is critical at all times.
Key Specifications for Industrial Optical Encoders
When choosing an optical encoder for industrial use, the specifications can significantly influence the encoder’s performance, durability, and suitability for your application. Understanding these specifications helps ensure the encoder will meet your needs effectively.
Resolution: Resolution refers to the number of distinct positions an encoder can detect within one revolution. Higher resolution means finer positioning accuracy. For applications that require high precision, such as CNC machines or semiconductor manufacturing, selecting an optical encoder with a high resolution is essential. Conversely, for applications with less strict accuracy requirements, a lower-resolution encoder may suffice.
Speed and Frequency Response: Speed is a critical factor, particularly in high-speed applications. The encoder must be capable of responding to rapid movements without signal degradation. For industries like automotive or robotics, where high-speed operation is standard, selecting an optical encoder with a fast frequency response is crucial to ensure the machine’s performance remains consistent.
Signal Output: Optical encoders can output various types of signals depending on the type of system and application. The most common output types are TTL (Transistor-Transistor Logic) and HTL (High-Threshold Logic). Each signal type has its advantages, depending on the control systems used in your machinery. TTL is typically used for lower-speed applications, while HTL is more robust and suitable for high-speed, industrial environments.
Sealing and Protection: Essential for Harsh Environments
Industrial environments often expose machinery to harsh conditions, including high temperatures, moisture, dust, and vibration. Optical encoders designed for industrial Automation use must have proper sealing to protect their delicate components.
Sealed Optical Encoders: Sealed optical encoders come encased in protective housings that safeguard them from contaminants, moisture, and dirt. These are ideal for environments like machine shops or factory floors where exposure to debris and liquids is common.
Exposed Optical Encoders: While not as protected as sealed encoders, exposed optical encoders typically offer higher accuracy and performance. These are generally used in environments where contamination is minimal, such as cleanrooms or semiconductor manufacturing facilities.
Mounting and Installation Considerations
The installation and mounting process is another important factor to consider when selecting an optical encoder. Encoders must be mounted securely to maintain optimal performance and prevent malfunctions. The mounting surface should be stable and rigid, as excessive vibration or misalignment can lead to encoder failure.
Shaft Type: Optical encoders come with various shaft types, including solid, hollow, and through shafts. The type of shaft you select will depend on your machine’s design and the specific application needs. Understanding which shaft type suits your machine’s setup is crucial for accurate readings and proper installation.
Mounting Method: Consider whether you’ll use a flange or a direct shaft connection when mounting the encoder. The mounting method can affect how easy the encoder is to install and maintain, as well as its ability to stay in place during machine operation.
Choosing the Best Optical Encoder for Industrial Use
Selecting the best optical encoder for your industrial application. boils down to understanding your specific needs and evaluating the available options. Below are some tips to help guide your decision:
Determine Your Application Needs: Whether you need a high-precision encoder for robotics or a rugged one for a machine tool, understanding your operational requirements is key. Recent advancements in optical encoder technology have led to significant improvements in both performance and flexibility. For precise positioning in manufacturing environments, an absolute optical encoder with a high resolution is usually the best choice. For high-speed applications, look for encoders with fast response times and high-frequency capabilities.
Environment and Operating Conditions: The environment in which the encoder will operate is crucial in choosing the right model. In dusty or wet environments, a sealed optical encoder is preferable. In a clean environment, such as semiconductor manufacturing, an exposed encoder may be more suitable due to its enhanced accuracy.
According to Coherent Market Insights (CMI), the global Optical Encoder Industry size is set to reach US$8051.6 million in 2032. Global Optical Encoder Industry will likely increase at a CAGR of 13.1% during the forecast period.
Evaluate Compatibility with Your System: Ensure the encoder you choose is compatible with your existing control systems and meets your feedback requirements. Whether you need TTL or HTL signal outputs, it’s essential to select an encoder that integrates seamlessly with your machinery.
Consider Longevity and Maintenance: Industrial optical encoders can vary in terms of durability. Choosing an encoder with a long service life and minimal maintenance requirements can help reduce the total cost of ownership (TCO). Encoders with features like predictive maintenance and self-diagnostics can reduce downtime and prolong the lifespan of your equipment.
Invest in Quality and Precision
Choosing the best optical encoder for industrial use is essential for maximizing system performance, reducing maintenance costs, and ensuring long-term reliability. By evaluating factors like resolution, sealing, environmental compatibility, and mounting methods, you can make an informed decision that meets the specific needs of your application. Whether you’re working with robotic systems, CNC machines, or semiconductor fabrication, investing in the right optical encoder ensures precise and efficient operation, ultimately leading to better productivity and lower operational costs.