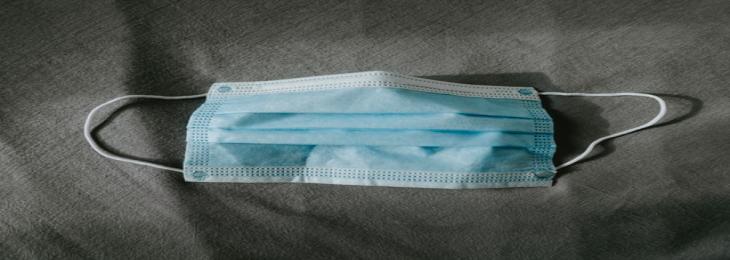
Scientists developed new process for fabricating small mask fibers and added them to cement concrete, making a stronger and more durable concrete
Disposable face masks became a non-degradable form of garbage causing environmental issues. Recycling these masks into useful material was approached previously in a study. Now a team of researchers at Washington State University developed a new method to use surgical face masks to create stronger and durable concrete. The team shredded the surgical masks into fibers and treated them with aqueous graphene oxide solution and mixed them into cement, which strengthens it and prevents it from cracking.
In earlier studies, it was found that adding small reinforcing fibers into concrete makes it less prone to cracks. In this new study the scientists explored used of polypropylene or polyester fabric in face masks to make fibers. The researchers removed the metal nose-bridges and ear loops from these face masks and then shredded the fabric that remains into fibers ranging in length from 5 to 30 mm. Further, the team treated these fibers with a solution of graphene oxide. This created a coating on them and added extra surface area helping them to bond with paste of Portland cement that is commonly used. The team added these fibers to cement which is the binding component in concrete at a volume of 0.1%.
Furthermore, the team of scientists tested the fiber-reinforced cement after a month of curing, and they found that the cement exhibited 47% more splitting tensile strength compared to Portland cement. As reported by the team, the fiber addition to the cement slightly lowered compressive strength by only 3%. With this research, the scientists demonstrated that diversion of used disposable masks from the waste stream to a high-value application is possible with one technology.