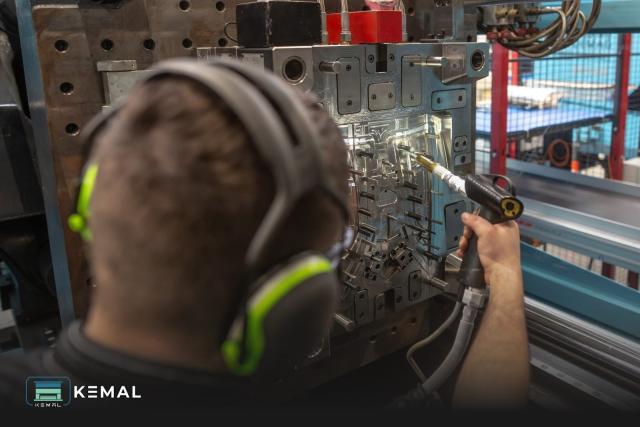
Injection molding is a manufacturing process used across various industries to create parts by injecting molten material into a mold. This technique has been a cornerstone of manufacturing for decades, offering numerous advantages that make it an essential choice for producing complex and high-volume parts.
Here, we will explore the reasons why manufacturers opt for injection molding, delving into its efficiency, cost-effectiveness, versatility, and the quality of the parts it produces. For instance, companies like www.kemalmfg.com specialize in providing top-notch injection molding solutions tailored to meet diverse industry needs.
Efficiency in Production
One of the primary reasons to use injection molding is its exceptional efficiency. Once the initial costs of designing and creating the molds are covered, the actual production process is incredibly fast compared to other methods. The ability to produce large quantities of parts in a short amount of time is a significant advantage, especially in industries where time-to-market is critical.
High Output Rate
Injection molding machines can produce parts at a remarkably high rate. Depending on the complexity of the mold and the material used, cycles can be as short as a few seconds. This high-speed production capability allows manufacturers to churn out thousands, if not millions, of parts within a minimal timeframe, dramatically reducing the production cycle.
Automation Potential
The injection molding process is highly automatable, with advanced machines handling the bulk of the production process. Automation not only speeds up manufacturing but also contributes to lower labor costs and enhances precision. Automated injection molding machines can operate 24/7 with minimal supervision, ensuring continuous production and reduced operational costs.
Cost-Effectiveness
Despite the high initial investment in mold design and tooling, injection molding is cost-effective, particularly for mass production. The longevity of the molds, which can be used for millions of cycles, disperses the initial costs over a larger number of units, significantly reducing the cost per unit.
Material and Resource Efficiency
Injection molding is also economically advantageous because of its ability to minimize waste. The process involves injecting the exact amount of material needed to fill the mold, which reduces excess and waste material. Moreover, any leftover or excess plastic can be recycled and reused, enhancing the overall efficiency of material usage.
Versatility in Materials and Design
Injection molding is compatible with a wide range of materials, including various plastics, metals (through die casting), and even newer composite materials. This versatility allows manufacturers to select the ideal material based on the strength, flexibility, color, and finish required for the final product.
Complex Part Design
The technique is particularly well-suited for producing complex and intricate parts. The high pressure used in injection molding ensures that the material fills even the smallest and most detailed features of the mold. This capability is vital for industries such as automotive, aerospace, and electronics, where component design can be complex and detailed precision is crucial.
Superior Quality and Consistency
The precision of injection molding also leads to superior quality and consistency among produced parts. Each part produced from the same mold will match the others with very little variation, ensuring uniformity across a production run. This consistency is essential for industries that require high reliability and tight tolerances, such as medical device manufacturing.
Enhanced Strength
The injection molding process allows for the use of fillers in the injection molds. These fillers reduce the density of the plastic while adding greater strength to the finished product. The use of such fillers can be tailored according to the specific requirements of the project, allowing for the production of parts that are robust yet lightweight.
Environmental Impact
In today's eco-conscious world, injection molding stands out for its potential to be a more sustainable manufacturing option. The ability to use recycled materials in the process is a significant plus, reducing the environmental impact associated with production. Moreover, the efficiency of the process itself, with minimal waste and energy usage, contributes to its sustainability.
The reasons to choose injection molding are clear: it is efficient, cost-effective, versatile, and capable of producing parts of excellent quality. Whether it's for automotive components, consumer electronics, or medical devices, injection molding offers a practical and reliable manufacturing solution that meets the demands of modern production landscapes. By continuously adapting to technological advancements and materials science innovations, injection molding remains a preferred choice for manufacturers worldwide, promising speed, precision, and profitability.
Frequently Asked Questions About Injection molding
What are the limitations of injection molding?
While injection molding offers many benefits, there are some limitations to consider. The initial setup cost can be high due to the need for creating precise moulds. Design changes can be costly once a mould is made. Also, while the process is suitable for high-volume production, it may not be cost-effective for very small production runs.
How much does it cost to start injection molding?
The cost of starting injection molding can vary significantly based on the scale of production and complexity of the parts being produced. Initial costs primarily involve purchasing or manufacturing the injection moulds and the machinery required. For small scale production, this can be tens of thousands of dollars, while large-scale operations can require investments in the millions.
What materials can be used in injection molding?
Injection molding is compatible with a wide range of materials including various plastics like polyethylene, polypropylene, ABS, and nylon. It's also possible to use silicone, rubber, and certain metals in specialized processes like metal injection molding (MIM). Each material offers different properties and must be chosen based on the requirements of the final product.
How long does an injection mould last?
The lifespan of an injection mould depends on several factors including the material it is made from, the design of the part, and the material being moulded. Typically, a standard steel mould can last for up to a million cycles or more. Aluminum molds are less durable, suited for shorter runs.
Can injection molding be environmentally friendly?
Yes, injection molding can be environmentally friendly, especially when manufacturers incorporate sustainable practices like using recycled materials and optimizing production cycles to minimize waste. Advances in biodegradable plastics and the recycling of post-industrial plastic waste also enhance the sustainability of this manufacturing process.