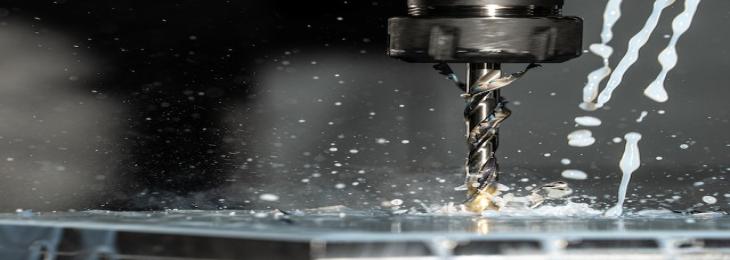
Computer numerical control technology is crucial to many areas of manufacturing today, and it’s also an area that’s little understood outside of specialist areas.
For any casual observers who are interested in what CNC brings to the table, here’s an overview of all the key facts and talking points.
The first CNC machines emerged in the 1950s
Although a degree of automation had been possible in manufacturing since the 19th century, it wasn’t until the mid-20th century that researchers at MIT were able to create the original CNC mill.
Today, a vast global market for CNC equipment and the associated technologies exists, and while there are several CNC programming languages out there, G-code is the most broadly deployed of the bunch.
CNC machinists need special training
Just because CNC equipment affords businesses a high degree of automation, there’s still a part to play for human workers.
Furthermore, the people who earn their keep working with CNC gear from day to day are not just low-skilled individuals, but rather highly trained and experienced professionals. With the help of the best used CNC milling machines at Revelation Machinery, experts in this field can make magic happen.
Precision is a major selling point
You might think that, as with a lot of mass production techniques, the main appeal of CNC tech is that it can work much faster compared with traditional craftspeople.
While this is true, the bigger benefit is arguably the level of precision that machinery can achieve. This is especially relevant in industries like aerospace, where incredibly tight tolerances make it impossible to settle for anything less than near-perfection.
Many types of materials are compatible
Depending on the type of machinery being used, it’s possible to work on materials as varied as steel, aluminum, plastic, composites and even glass.
This means that no matter the requirements of the project at hand, there’s a CNC machine out there which can meet them.
It’s not purely a subtractive manufacturing technology
For a long time, most CNC equipment worked by removing material from a larger workpiece. More recently, the rise of 3D printing, or additive manufacturing, has flipped the script on this state of affairs.
3D printers can work with an impressive array of materials as well, building up designs in layers and even making previously impossible creations achievable.
As well as 3D printing with plastics, there are even systems that can print in building materials, creating entire buildings with the help of good old CNC.
Safety is paramount
Another thing worth noting about CNC equipment, particularly of the modern variety, is that it is far safer than old-school equivalents or traditional manufacturing techniques.
By putting human operators out of the reach of danger, the likelihood of injuries and accidents is dramatically reduced.
Tooling doesn’t always make contact with the material
When you think of a CNC machine, it’s probably a mill or a lathe you’re picturing. But more recently the rise of laser-based solutions has changed how materials can be cut, etched, engraved and ablated.
Then there are water-based solutions, where a high powered jet of H2O in combination with abrasive particles can cut through even the thickest, toughest materials on the market.
This demonstrates the versatility and adaptability of the underlying CNC code, allowing it to remain relevant for decades.
Final thoughts
It might not be the most glamorous tech in the world, but CNC has stood the test of time and continues to facilitate the manufacture of all sorts of products. Even as other areas evolve, CNC looks set to stay the course and keep machine shops and factories ticking over.