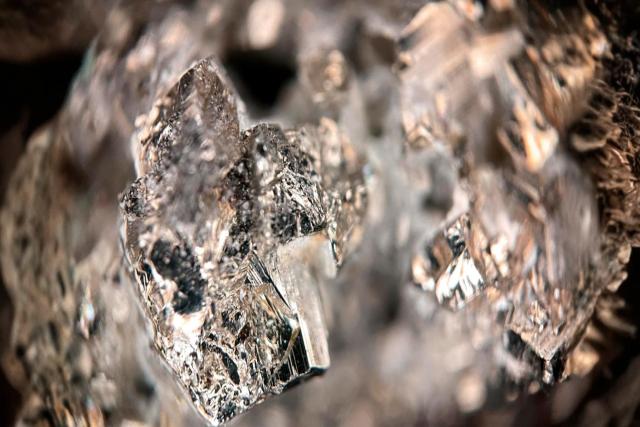
A metal of high demand with essential uses in the electronics, aerospace, and steel sectors, molybdenum is mainly reached through extraction and refining. It is more crucial to capture the intricacy of molybdenum refining as well as molybdenum extraction and the sustainability concern as the demand for the metal grows in various industries. To know more about Molybdenum industry check out the latest research report by Coherent Market Insights
Removal of Molybdenum
Molybdenum is found mostly as a byproduct during the extraction of copper. The only naturally occurring molybdenum minerals are molybdenite (MoS₂) and wulfenite (PbMoO₄). The molybdenum ores, which are generally accompanied by massive copper ore deposits, are initially separated in the process. Once the ore mining is completed, the ore is crushed into small fragments and powdered to finer particles to enhance its surface area for processing.
The most common technique of extraction is flotation, where chemicals and water are mixed with crushed ore and agitated together to cause the minerals containing molybdenum to float on the surface. Separation and drying, then refining further, results in molybdenum-rich concentrate.
Molybdenum Refinement
To obtain high-purity molybdenum, the extracted molybdenum concentrate undergoes a series of refinement processes. The first process of refinement is roasting, which converts molybdenite to molybdenum oxide (MoO₃) by heating the concentrate in oxygen. Sulfur and other impurities are removed during this step, making the concentrate a purer final product.
Then, for obtaining pure metal of molybdenum, the oxide of molybdenum is subjected to a high heat and treated either with carbon or hydrogen. What results is an ultra-fine powder that, depending on how it will be used in industry applications such as in electronics and the production of steel, will then be converted further into its various forms such as rods, sheets, or powder.
Challenges to Continuous Mining of Molybdenum
Molybdenum processing and mining are environment degrading, like all mining. Soil erosion, water contamination, and loss of habitats are all by-products of mining operations. Flotation involves a lot of water, and toxic constituents can be present in the tailings—waste product after processing, which can negatively affect the ecosystems around it. The other emissions related to refining include sulphur dioxide, which, when not properly regulated, will result in acid rain and air contamination. Further, the environmental impact of molybdenum production is escalated by the great energy use involved in mining and processing, particularly when alloying molybdenum with other metals for various applications.
Recycling molybdenum from scrap is becoming more popular as a greener method. It requires lower energy and resources than recovering the metal from ore. Recycled molybdenum is thus a greener way to supply the increasing demand for the metal.
Molybdenum is difficult to refine and extract and requires a huge number of resources. While the metal is extremely important to a wide range of high-performance applications, the extraction and refining steps create severe environmental concerns. Yet with continued development in sustainable methodology, including more efficient water usage, cleaner processes, and expanded utilization of recovered molybdenum, the industry is slowly moving in the direction of reducing its footprints on the environment without forgoing fulfilling worldwide demand.