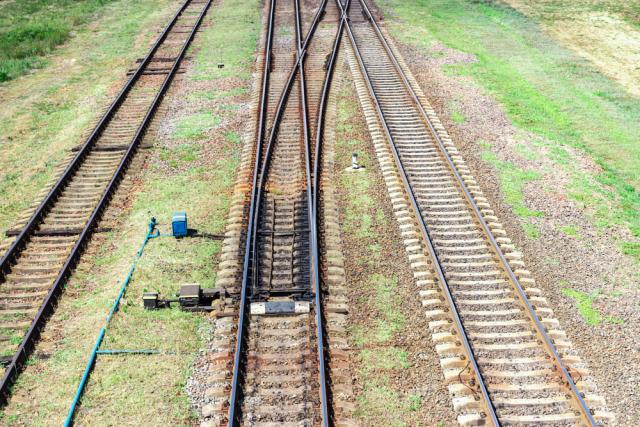
Railway connectors are the essential components in modern rail system. These connectors ensure robust, continuous and mechanical connection between the different railway components. These components includes tracks, signalling systems, and trains. The designing process of railway connectors face several challenge while engineering and material. These connectors are designed to withstand in harsh and demanding environments. These are important for those connectors that can work in extreme weather conditions, corrosion, high temperature, and mechanical stresses. This blog post provides an overview on the challenges faced by the manufacturers while designing the railway connectors. For deep understanding in the global railway connectors market explore the report published by Coherent Market Insights.
- Extreme Weather and Temperature Variations: These connectors are exposed to a wide range of temperature ranging from the freezing cold in winter to scorching heat in summers. These factors will put a strain on the materials used in the connector designs. They are not only used to maintain performance across the temperature spectrum but also helps in avoiding failure due to thermal expansion and contraction. These train connectors are design to deal with temperature that could otherwise degrade the integrity of standard materials.
- Corrosion Resistance in Moisture-Prone Environments: Corrosion is one the major limitation in the field of railway connectors. It comes especially in areas of high humidity, coastal regions, and locations where salt from snow and road treatment is needed. To make the corrosion-resistant railway connectors, companies are now using those material that can withstand in prolonged exposure to moisture and harsh chemical. It is also used to prevent failure that could jeopardize to entire in the railway systems. This consists the use of coated connectors, special alloys design to prevent corrosion. These connectors will be sealed from dirt, moisture, environmental containments to ensure the long-term durability. These seal will resulted to accelerate wear and reduce connector’s lifespan.
- Mechanical Stresses and Vibration: Railway connectors are effected by the mechanical stress that is caused by the constant pressure, movement, and vibration comes from the operation of trains. Mechanical forces and environment factors including humidity and wind make the connectors to build with exceptional durability. Harsh environment railway connector are designed with the feature such as flexible material, secure locking mechanism, and vibration damping. These features will aid in preventing loosening and disconnection made due to constant shaking and movement.’
- Ensuing Electrical Reliability: It is important for railway connectors to maintain reliable electrical conductivity despite of exposure to environment challenges. Dirt, temperature, and moisture will lead to corrosion, insulation breakdown and other issues that will restrict the connector’s electric performance.
- Innovative Materials and Manufacturing Techniques: To overcome the issues that are posed by the harsh environment. Manufacturers need to design connectors for extreme railway conditions and innovative in the selection of material and its production techniques. Innovation made in the material science will lead to the development of ceramics, alloys, and polymer composite. This new advancement will lead to provide resistance to corrosion, wear and tear, temperature.