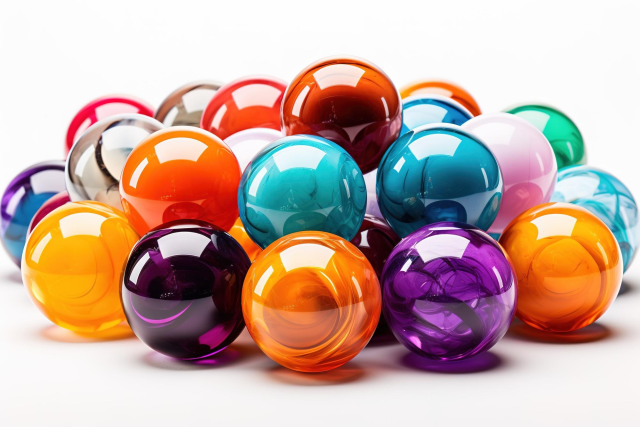
The Industry for thermoplastic elastomers is witnessing increasing demand as industries seek to utilize them in new and innovative uses. This blog talks about the advantages, characteristics, and flexibility of Thermoplastic Elastomers, and why they are a game-changer in diverse industries.
Advantages of Thermoplastic Elastomers: Why TPEs Are Gaining Popularity
The benefits of thermoplastic elastomers are realized in varied industries. TPEs exhibit a unique combination of the moldability of plastic and rubber elasticity, thus well-placed to support varied uses. The simplest yet most apparent benefit is how they can be processed and re-molded, which facilitates complex designs at low effort by the manufacturer. In contrast to conventional rubber, which needs elaborate curing operations, TPEs can be melted and molded several times without shape or performance loss.
TPE vs Conventional Rubber: A Clear Advantage
Comparing thermoplastic elastomers to conventional rubber, it's no wonder TPEs are usually the better option.
In addition, TPEs give more consistent production. Unlike rubber, which may have varying performance levels between batches because it depends on the curing agents and other additives, TPEs are more consistent. This implies manufacturers can achieve consistent results in raw materials and end-products.
Another significant benefit is that TPEs are more environmentally friendly than conventional rubber. TPEs are recyclable, whereas conventional rubber tends to be non-recyclable and can be a source of environmental waste. TPEs are also simpler to process, using less energy and resources to produce, thus lowering their overall environmental footprint.
Benefits of Thermoplastic Elastomers in Different Applications
The benefits of thermoplastic elastomers make them a very suitable material of choice for several industries. In the automotive industry, for instance, TPEs are applied to parts like seals, gaskets, and trim components.
In the health industry, TPEs are finding increasing uses for medical tubing, catheters, and other healthcare applications. TPE is free of latex, thus becoming a safer product to use by individuals who suffer from latex sensitivities. Moreover, TPE can be easily sterilized, an important fact given that its intended use will take place within environments that highly prioritize cleanliness in health settings. TPE also remains soft and pliable in form, rendering the patient comfortable should it find usage in any devices used to enter the body in direct contact.
Thermoplastic Elastomers Properties: One in the Same When It Comes to Flexibility and Durability
Thermoplastic elastomers possess an extensive array of characteristics that make them suitable for demanding applications.
TPEs also have great chemical resistance, enabling them to be resistant to exposure to oils, greases, and other aggressive chemicals that are typically encountered in industrial settings. They can withstand a broad spectrum of temperatures without compromising their performance, which makes them flexible for application in both hot and cold temperatures.
Another significant attribute of thermoplastic elastomers is their ability to maintain performance and shape during aging. Compared to traditional rubber, which depreciates quickly in the long term as it reacts to environmental forces, TPE is resistant to wear out and deformation, conferring its elements with longer durability.
TPE Recyclability and Durability: A Green Solution
This renders TPEs of interest to those Industrys interested in waste reduction and sustainability. TPEs can be used and recycled dozens of times without a drop in their capabilities for performance, making it an incredibly sustainable material choice.
Furthermore, TPEs are very tough. They weather, UV, and harsh chemicals, so products that are produced using TPE can be exposed to the outside environment for extremely long periods of time and not degrade. This renders them extremely useful for use in automotive applications, for instance, where components are exposed to extreme environments such as heat, vibration, and exposure to greases and oils.
TPE versus Rubber in Industrial Usage: Efficiency and Performance
Industrial applications place maximum importance on the efficiency and performance of the material in terms of ensuring that the parts operate optimally and long enough.
Compared to conventional rubber, TPEs are satisfactory in the majority of applications. TPEs can be processed faster and with less investment, hence a more efficient material for large-scale production. This results in reduced costs of production and quicker turnarounds.
In performance, TPEs are generally best suited for use in industry owing to their remarkable elasticity, resistance to chemicals, and toughness.