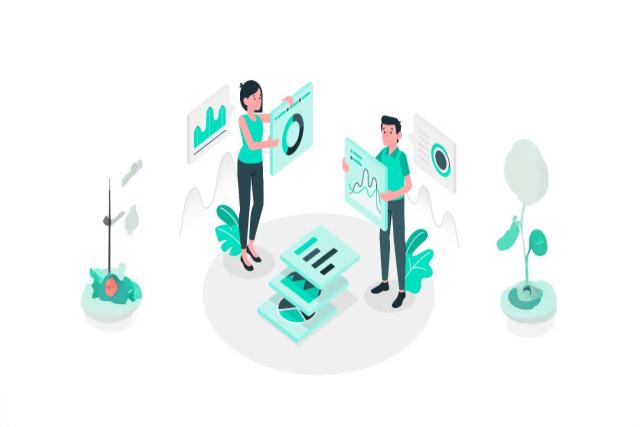
Predictive maintenance with digital twin is a game-chain for industries that want to limit downtime and promote operating efficiency. Traditional maintenance is done as a reaction to planned maintenance or repair, resulting in unnecessary expenses and unplanned failures. With digital twin predictive maintenance, however, the game is altered, enabling one to monitor in real-time, forecast failures, and take decisions based on facts.
Learning about Digital Twin Predictive Maintenance
A digital twin is a virtual replica of a system, process, or physical asset that is updating in real-time constantly. With IOT-based analytics combined AI-based future, with maintenance maintenance, industries can simulate their asset behavior, detect discrepancies, and predict failures in advance.
Industries apply digital twins for health monitoring in manufacturing, energy and healthcare industries to expand their asset lifespan and maintain maintenance programs in sinks. The result is reduced to downtime, low operational costs and high efficiency.
Major benefits of digital twin predictive maintenance
1. Initial discovery of defects and low downtime
Digital twins enable the future maintenance by using digital twins that this sensor continuously examines data. The AI-based algorithm detects the pattern of wearing and tear, enables the maintenance personnel to take action in advance to improve it.
In manufacturing, for example, a digital twin of a manufacturing line can detect abnormal vibrations in a machine, triggering a preventive maintenance signal before total breakdown.
2. Cost savings and resource efficiency
Reactive maintenance means unplanned repair and waste of time in production. Digital twins allow infections for preventive maintenance, ensuring that the repair requires real -time data.
In energy power plants, digital twins monitor the performance, leading to maintenance schedule to prevent expensive shutdowns. This increases efficiency and profits.
3. IOT and digital twins for equipment monitoring
The combination of IOT sensor and digital twins enables to monitor real -time by continuously collecting and analyzing operating data. This is particularly beneficial in industries where uptime is important, such as healthcare and transport.
For example, hospitals use digital twins to track the performance of MRI machines and CT scanners, making them predict potential failures before affecting the patient's care.
4. Smart decisions AI-Interested Future Maintenance
Artificial intelligence increases digital twins by improving the accuracy of predictions of failure. The AI models analyze both historical and real -time data, allowing businesses to refine their maintenance strategies for greater efficiency.
For example, in automotive manufacturing, AI-operated digital twins simulate vehicle components wearing and tears, helping manufacturers help manufacturers to streamline the supply chain management and reduce the spare part cost.
Real world case study: digital twin applications in manufacturing
A major global automotive company integrated digital twin techniques in its manufacturing process for monitoring robotic assembly lines. By analyzing real -time performance data, the company successfully reduced the machine downtime by 30% and increased the device lifetime by 25%.
The strategy of this future maintenance not only reduced the cost of maintenance, but also improved overall productivity and workplace security.
The future of digital twins
The next phase of digital twin predictable maintenance will be inspired by progress in AI, IOT and machine learning.
To achieve deep insight on how digital twins are changing, find out our broad digital twin market guides. Additionally, learn how AI and IOT are re -shaping digital twin solutions to power the next generation forecasted maintenance strategies.
Digital twin can achieve more efficiency, low cost, and increased reliability by embracing predictable maintenance. Since digital twin techniques move forward, business adopting these innovations will lead to a significant competitive edge.