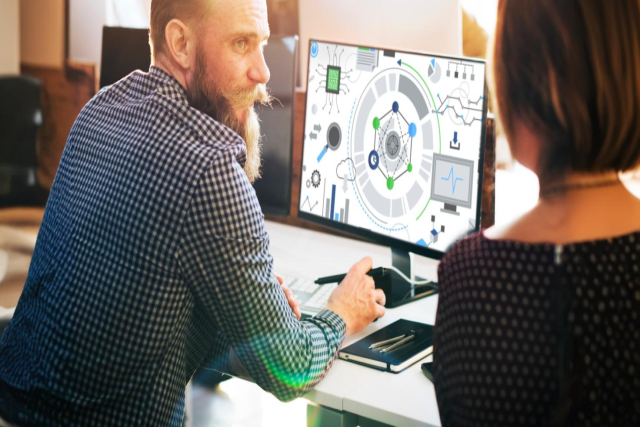
Asset management is significant in industrial activities to ensure performance, minimize operation expenses, and prolong the lives of equipment and machines. To achieve maximum asset life cycle management, a Computerized Maintenance Management System (CMMS) is required since it eases such operations as tracking of assets, maintenance scheduling, compliance, and analysis of data. Organisations can leverage a CMMS to effectively extend the life of their assets, enhance operating effectiveness, and promote compliance with industry regulations. To explore more about computerized maintenance management system industry check latest research report by Coherent Market Insights. The ways in which a CMMS can improve asset lifecycle management:
- Enhanced Asset Tracking and Monitoring
Asset tracking is one of the primary functions of a CMMS. The technology allows businesses to monitor the performance, condition, and location of all assets in real-time.A CMMS maintains a complete history of every asset by aggregating its information, such as warranty information, maintenance history, manufacturer's specifications, and usage. With this accurate information, maintenance staff can make sound decisions about whether to repair, refurbish, or replace assets, avoiding unexpected breakdowns or downtime.
Besides, with a CMMS, businesses are able to keep track of assets' condition and age so that they can flag equipment that should be replaced or refurbished before having a disastrous failure at an unreasonable cost.
- Schedule maintenance in advance.
A CMMS is required to maximize maintenance scheduling and ensure that assets are being maintained on a regular basis as per manufacturer guidelines. Routine maintenance can be maximized on a time, usage, or condition basis by companies using tools such as automated preventive maintenance (PM). This preventative action minimizes the risk of equipment failure, decreases the likelihood of unscheduled downtime, and, ultimately, optimizes asset life.
For instance, a production firm can use a CMMS to schedule routine checks on 24/7 machines. Routine preventive maintenance can lead to early discovery of issues such as wear and tear on essential parts, where they can be fixed before escalating into costly repairs or downtime.
- Data-based asset replacement and optimization decision-making.
Assets also wear out with time, and their efficiency reduces. A CMMS provides firms with information-based insights from data gathered through equipment performance and history of maintenance. By analyzing the data, firms can know whether an asset's useful life is approaching an end and whether to replace, repair, or upgrade the asset at a lower price.
For instance, in case the CMMS reveals that a machine has to be frequently repaired, underperforms, or uses excess energy compared to planned, replacement might be less expensive than repeated expenditure on maintenance.
- Compliance with industry regulations.
Assets in most industries, especially those with safety-critical processes (e.g., manufacturing, healthcare, and oil and gas), have to comply with some legal and safety standards. A CMMS enables businesses with regards to compliance by maintaining detailed records of all inspections and maintenance on assets. It is particularly relevant to audits and inspections because a CMMS is capable of reporting regulatory compliance.
Companies can prevent penalties, fines, and lawsuits against noncompliance by making compliance operations automatic like ensuring assets are due for planned testing and inspection.
- Cost effectiveness and asset lifecycle planning.
A CMMS also provides both the maintenance cost and capital cost of each asset, which is needed to make asset lifecycle decisions over a longer-term. Organizations can, for instance, make informed decisions on whether to retain or replace an asset based on its TCO over the total lifespan. The CMMS also assists businesses to budget and make plans for future investments based on repair costs, downtime charges, and the actual cost of replacing assets.
Computerized maintenance management system (CMMS) is an effective technique used to facilitate asset lifecycle management. CMMS solutions assist businesses in the maximization of asset lifespan, minimizing downtime, and overall asset efficiency maximization through improved asset tracking, predictive maintenance scheduling, decision-making based on facts, and ensuring adherence to industry regulations. Moreover, through real-time performance data and predictive maintenance features, a CMMS enables businesses to take a more strategic approach towards asset management, resulting in cost savings, better operational performance, and long-term longevity.