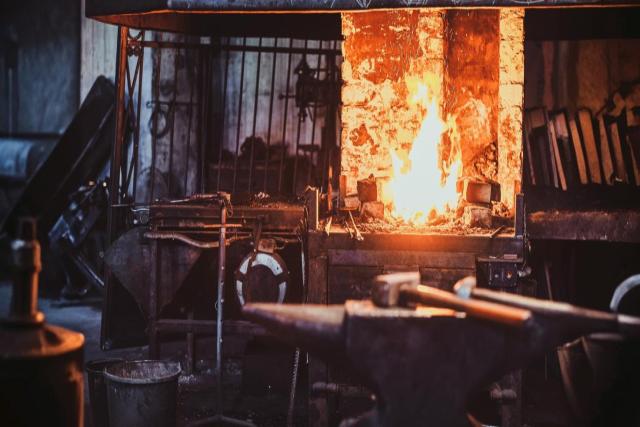
Forging is a critical process in automotive sector involving toughness, strength, and precision. Forging, being metal shaping via the application of high pressure or temperature, creates products not just to be tough but extremely reliable as well, thereby making forging a vital ingredient within automobile manufacture. The forging technology has extensively been applied in the manufacture of automobiles because it has the capability of producing strong, high-quality parts that can withstand harsh environments.
Advantages of Forging in Automobile Manufacture
- Immense strength and hardness
One of the greatest reasons that forging is extremely common in the automotive industry is that it gives added strength to the components. When the metal is forged, it is being compressed under extreme pressure, and it aligns the grain structure in the process. This creates denser, tougher components compared to machined and cast components. In automobiles, it means forged components can be designed to meet rough conditions such as high temperature, overloading, and usage that make their strength increase as time passes.
For example, forged car engine components, such as crankshafts and connecting rods, can withstand extraordinary mechanical stress.
- Increased precision and accuracy.
Forging allows extreme precision and accuracy while manufacturing components.
The pressure applied in the forging process is intensive, and this minimizes material wastage while allowing close tolerances in the end product. It is particularly beneficial in the automotive sector, where accuracy must be preserved to get the vehicle moving and for safety purposes. Gears, suspension parts, and brake discs have to be made extremely accurately to run properly and safely. Counterfeit parts can easily be mixed with other car parts without the need for post-processing and a possibility of defect or failure.
- Weight reduction and efficiency.
In the automotive sector, minimizing weight while not sacrificing strength is critical in enhancing fuel economy and vehicle performance. Forging allows companies to produce lightweight components without compromising toughness. This is especially critical in automobile manufacturing parts like engine blocks, chassis, and wheel rims, where weight reduction can help enhance the overall efficiency and performance of the vehicle.
Uses of forging in the automobile sector are:
- Engine parts.
Forging is one of the major processes of manufacturing engine parts of vehicles. Connecting rods, crankshafts, and pistons are regularly forged to resist high pressure, heat, and constant mechanical strain. Engine parts manufactured using forging are more hard and stronger in nature, and thus they enhance the performance, durability, safety, and overall development of a vehicle.
- Suspension and steering parts
Suspension and steering parts like control arms, spindles, and tie rods are also extensively forged to obtain high strength as well as wear resistance. Such elements play a significant role in vehicle stability and handling as they carry the weight of the vehicle as well as absorb shock from the road.
- Automotive wheels.
Forcing wheels, especially high-performance wheels, is most often utilized to achieve the proper strength-to-weight ratio. Forged wheels are also lighter and stronger compared to cast wheels, and this improves the performance of a car, fuel economy, and safety. Precision of the forging process also results in wheels that are less susceptible to load cracking or failure.
Forging is an important process in the automotive sector, with several advantages due to forging as increased strength, durability, precision, and weight reduction. Its capability to produce durable, high-quality components is crucial to the performance, safety, and functionality of modern vehicles. Forging auto parts, from motor parts to wheels, makes them last and perform at their best levels, fulfilling stringent manufacturers' and consumers' requirements.
Sources:
Company: Zetwerk, Dragon work
Profit Organization: Research gate