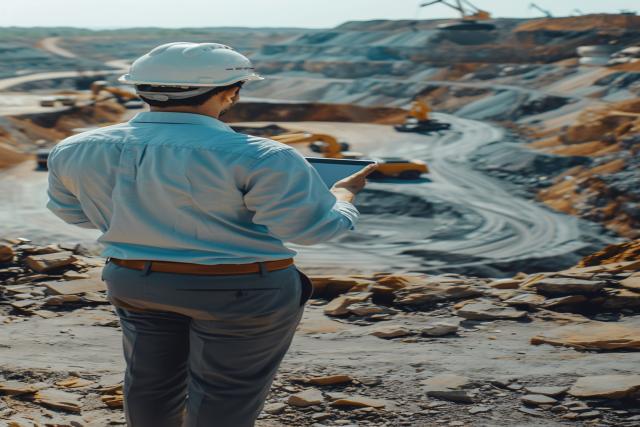
Fluorspar has become a crucial industrial mineral used in metallurgy and chemical manufacturing. It is generally used for producing hydrofluoric acid. Similarly, it finds application in steelmaking and aluminum production.
How is fluorspar industry performing? According to Coherent Market Insights, the global fluorspar industry is set to register a CAGR of 4.6% during the forecast period, totaling US$ 3 billion by 2030.
Despite its widening applications, fluorspar mining and processing poses significant environmental and safety challenges. To address this, effective management is essential. Fluorspar mining hazards can be tackled by using different technologies and methods.
Environmental Impact of Fluorspar Extraction
Land Degradation
Fluorspar extraction often leads to deforestation and soil erosion. Large forests are cleared to access fluorspar deposits. It also results in the destruction of habitat as deep pits are made during the excavation process.
- To mitigate these
- Use sustainable fluorspar mining
- Employ land reclamation strategies like reforestation
- Conduct environmental impact assessment before starting projects
Water Pollution
Fluorspar mining operations produce wastewater containing fluoride and other heavy metals. This can contaminate local water sources, posing health risks to humans and animals.
Fluorspar processing also generates large amounts of wastewater with similar contaminants. Proper wastewater treatment and disposal are key to mitigating environmental impact of fluorspar mining and processing.
-
- To mitigate water pollution
- Employ advanced wastewater filtration systems to remove contaminants
- Treat wastewater to remove unwanted contaminants
- Implement strict recycling measures
- Monitor water quality regularly
- To mitigate water pollution
Air Pollution
Fluorspar mining and processing also lead to air pollution. Fluorides and silica dust are released into the air during drilling, blasting, and crushing. Fluorspar processing can release harmful gasses like hydrogen fluoride and sulfur dioxide. This can badly affect air quality.
- To mitigate this
- Employ dust suppression techniques like water spraying
- Implement strict recycling measures
- Monitor air quality regularly to ensure compliance with regulatory standards
Waste Generation
Fluorspar processing generates tailings, sludge, and other waste materials which may contain hazardous substances. As a result, fluorspar waste management becomes necessary.
-
- To mitigate this
- Store tailings in secure impoundments
- Treat waste materials to neutralize hazardous substances
- Focus on using waste materials
- To mitigate this
Safety Considerations
Exposure to Toxic Compounds
Prolonged exposure to airborne fluorides can lead to complications like lung diseases. It may even cause skeletal fluorosis in some cases, causing pain and stiffness in bones and joints.
- To mitigate this
- Use personal protective equipment like masks and gloves
- Ensure proper ventilation in fluorspar processing plants
Structural Hazards
Underground fluorspar mining poses risk of rockfalls and cave-ins. These dangers arise from the unstable nature of rock structures in the mine.
- To mitigate this
- Conduct regular geotechnical assessments
- Employ support structures in mine tunnels
Chemical Hazards
During fluorspar processing and usage, many chemicals are used or formed. These chemicals can be dangerous for workers, causing burns and poisoning.
- To mitigate this
- Use protective clothing
- Utilize proper storage solutions
Improving occupational safety in fluorspar industry is necessary to protect workers and equipment. Companies need to use eco-friendly fluorspar processing methods as well as comply with regulations for fluorspar mining.
New research is being carried out into synthetic alternatives to natural fluorspar. Researchers are exploring synthetic fluorspar production form industrial waste products like phosphogypsum. This will not only help to meet fluorspar demand but also reduce waste was well.
Recycling used fluorspar is also gaining traction. New techniques are being explored to regenerate fluorspar from used hydrofluoric acid and the slag.