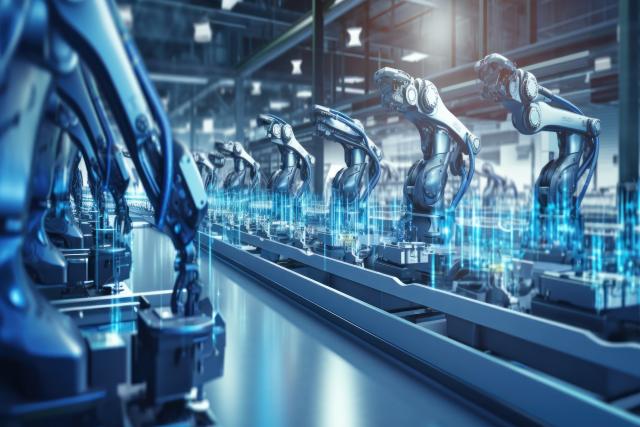
Let’s take the case of surgical instruments. Medical device contract manufacturers have to follow safety instructions and assemblies as per industry IFU (Instructions for Use). The global medical instruments and devices sector is projected to increase to USD 192.3 billion by 2030, growing at a CAGR of 10.2% from 2023 to 2030. As international benchmarks are shifting, contract manufacturers must already engage with FDA and ISO requirements for quality control in medical device production. Let’s explore the major challenges with regulations and how manufacturers tackle them.
Universal Regulatory Constraints
Medical device contract manufacturers must comply with strict legal regulations such as FDA rules, ISO 13485 certification, and the EU's MDR (Medical Device Regulation). For instance, domestic manufacturers in the USA must adhere to FDA 21 CFR Part 820 regarding quality systems, while those in Europe must comply with the MDR system to obtain CE marking approval. Any noncompliance increases the likelihood of product recalls, legal complications, or financial losses.
Ensuring Compliance While Screening for Violations
To follow global standards, detailed regulation of quality management systems (QMS), meticulous documentation, and process validation are crucial. Leading manufacturers invest in compliance tracking and maintain real-time regulatory intelligence teams to monitor policy changes. An ISO 13485-certified contract manufacturer specializing in surgical instruments adopted these methods to enhance compliance in manufacturing processes, ultimately securing faster commercialization approvals for their clients.
Quality Control in Medical Device Production and Its Significance
Defect-free and precise production of medical devices is essential for building trust and ensuring regulatory safety compliance. This includes real-time monitoring, defect tracking, and automated inspection processes. For example, a diagnostic device manufacturer implemented automated defect detection processes, reducing the FDA-reported defect rate by 40% per year.
The Changing Regulatory Terrain
Constant changes in medical regulations require manufacturers to stay updated. Emerging trends include post-commercialization surveillance, cybersecurity regulations for connected devices, and sustainability measures as new industry standards evolve. Many European manufacturers faced challenges transitioning to MDR due to its more stringent approval processes. However, contract manufacturers that proactively adapted early gained a strategic advantage, positioning themselves as industry leaders when compliance strategies were enforced.
Conclusion
The medical device manufacturing sector evolves rapidly. Outsourcing firms must continuously allocate resources for R&D, quality control, and compliance with FDA and ISO norms. By adopting proactive compliance strategies, contract manufacturers can significantly reduce operational and industry risks while ensuring long-term success in the healthcare sector.