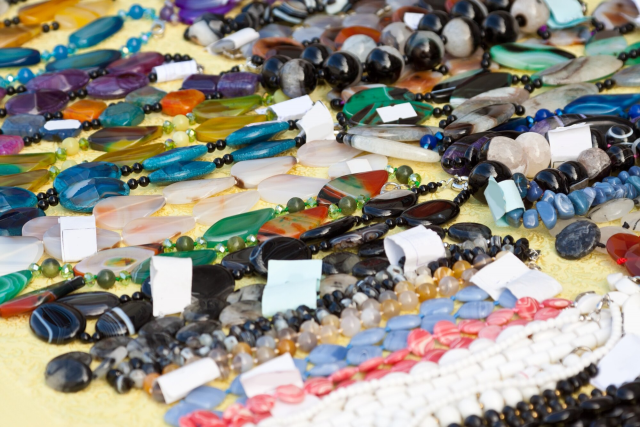
Thermoplastic elastomers (TPE) have become a revolutionary material in the automotive sector, providing a blend of properties from plastics and rubber. With the automotive industry still looking for means to improve vehicle performance, minimize weight, and increase sustainability, TPEs have gained popularity because of their versatility and better physical properties.
TPE Automotive Applications: Driving Innovation in Production
Thermoplastic elastomers have been widely used across many automotive applications and are now an integral part of the fabric of contemporary vehicle design. Owing to their higher flexibility, durability, and processability, TPEs are most suitable for making automotive components that require resilience, along with retention of shape when exposed to hostile conditions. From under-the-hood components to interior and exterior uses, thermoplastic elastomers have established themselves as a means to improve vehicle performance and appearance.
One of the most important reasons why TPEs are most preferred in auto manufacturing is because they can hold up under aggressive environments. They can retain their properties when used at high temperatures and never degrade from exposure to oil, grease, and fuels that are prevalent in most car conditions.
Automotive Components Produced by Thermoplastic Elastomers: A Versatile Range of Applications
Thermoplastic elastomers find application in producing a broad array of automotive components, each of which is important for the vehicle's performance and appearance. Some of these components include airbag covers, constant velocity joint boots, and weather seals, among others. TPEs provide enhanced flexibility, which is critical for components such as seals and gaskets, to keep them intact while subjected to pressure or in repetitive movement.
Apart from their mechanical applications, TPEs are also applied in the production of interior aesthetics and functionality parts. These parts include armrests, seat cushions, and dashboard trim. The softness of the TPE surface offers not only better tactile comfort to the driver and passengers but also enhances the vehicle's luxury feeling and overall comfort.
Thermoplastic Elastomers in Car Production: Automaker's Key Benefits
The vehicle industry has, for many years, made use of thermoset rubbers in some of its parts, but TPEs are gaining popularity for taking their place since they have been more processable and offer enhanced properties.
The lightness of thermoplastic elastomers also has the added advantage in the drive toward fuel efficiency and lower carbon emissions. Through substitution of heavier products such as metals and thermosets, TPEs become part of a vehicle's total weight savings. Weight savings improve fuel economy, reduce emissions, and enhance vehicle performance overall, all of which fit into the industry's long-term push toward more sustainable transport solutions.
Advantages of TPE in the Automobile Industry: Sustainability and Performance
The use of TPEs in the manufacture of automobiles has many advantages for automakers, especially with regards to performance, design freedom, and environmental sustainability. The greatest advantage of TPEs is their superior impact resistance, which makes them perfect for application in high-stress automotive components such as bumpers and trim components. These parts are constantly being impacted, and TPEs guarantee that they retain their shape and functionality in the long term.
Another major advantage of TPEs is their resistance to harsh environmental conditions, such as extreme temperatures, UV radiation, and chemicals. This renders them a very good option for automotive uses exposed to outdoor factors, including exterior trim, seals, and gaskets. TPEs provide long-term wear and tear resistance, extending the lifespan of components in a vehicle.
TPEs also contribute to the reduction of vehicle weight, which is increasingly relevant in terms of fuel economy and carbon reduction. Lightweight materials need to be used to decrease a vehicle's overall weight, which can lead to improved fuel efficiency and reduced environmental footprint. TPEs are also used in many applications to drive this function, ranging from under-the-hood parts, interior parts, and structural parts.
Moreover, TPEs are easy to process and can be moulded into complex shapes easily, with greater design flexibility by car manufacturers. Such a facility to manufacture fine designs without the loss of quality is one such major reason the automobile industry uses more TPEs.
Thermoplastic Elastomers for Vehicle Parts: The Future Directions and Innovations
As the auto industry continues to evolve, thermoplastic elastomers will increasingly be a factor in designing car parts for the future. Electric vehicle (EV) demand is also expected to continue boosting TPEs since the EVs require light yet strong, eco-friendly materials in manufacturing.
In addition, advances in TPE formulations are making possible the creation of even more sophisticated materials designed for particular automotive applications. For instance, novel TPE grades with improved flame retardancy, chemical resistance, and even self-healing capabilities are being investigated to address the evolving requirements of modern automotive production.