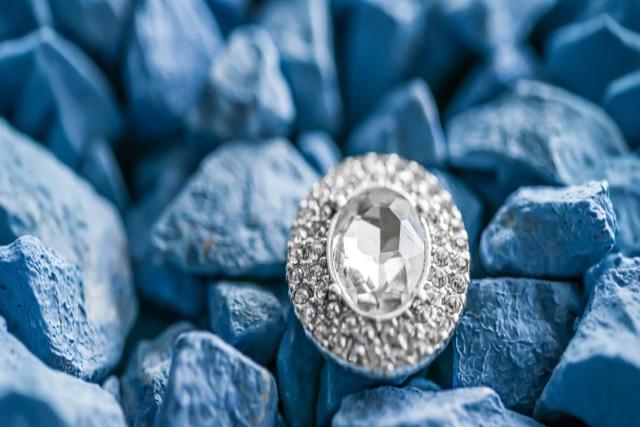
Synthetic diamonds, also referred to as lab-grown diamonds, are an example of man’s creativity and innovation in replicating nature’s wonders. They are made by using advanced techniques, such as chemical vapor deposition (CVD) and high pressure and high temperature (HPHT).
Lab-grown diamonds are identical to natural diamonds in both appearance and composition. However, some synthetic diamonds exhibit superior hardness and higher thermal conductivity compared to many naturally formed diamonds. This is because they are produced under controlled conditions.
Synthetic diamonds are widely used in the industrial sector for applications like cutting and drilling. Companies use technologies like CVD and HPHT to create customized diamonds that meet rigorous demands of industrial cutting and drilling.
What is the demand outlook for synthetic diamonds? According to Coherent Market Insights (CMI), global demand for synthetic diamonds is set to rise at 7% CAGR during the forecast period. Total industry size will likely reach US$ 38.78 billion by 2030. Rising adoption of high-precision synthetic diamond tools in industrial applications like cutting and grinding will likely shape this future growth.
Why Synthetic Diamonds for Industrial Applications?
Synthetic diamonds are gaining wider popularity across industrial applications due to their
- Sustainable and eco-friendly nature
- Low cost
- Easy availability
- High purity
Rising emphasis on reducing environmental exploitation due to diamond mining is putting synthetic diamonds into the limelight. Similarly, their cost-effectiveness and wider availability are encouraging industries to use these lab-grown diamonds.
Many industries are shifting their preference towards synthetic diamond-based tools. In the synthetic diamond vs natural diamond tools comparison, the former appears to be the winner, courtesy of rising demand for high-performance and sustainable industrial tools. Their cost-effectiveness also makes them attractive options for drilling and cutting applications.
Industrial Uses of Synthetic Diamonds
- Synthetic Diamond Cutting Tools
Synthetic diamonds are widely used in cutting tools. This is due to their tendency to improve precision, efficiency, and durability. They are incorporated into diamond-tipped drill bits and saws.
Polycrystalline diamond (PCD) cutting tools are employed for machining hard metals such as titanium and tungsten carbide. These tools find applications across electronics, automotive, and aerospace industries.
Diamond blades are extensively used for cutting glass, ceramics, and semiconductor wafers. They are also becoming ideal for precision cutting of gemstones. Diamond-coated cutting tools have the tendency to cut through hard materials like concrete, granite, and marble.
There are various advantages of synthetic diamond cutting tools. These include high cutting efficiency, optimal hardness, better accuracy, durability, and cost-effectiveness.
- Synthetic Diamond for Drilling Applications
Synthetic diamonds are also replacing natural diamonds in drilling applications. They are being widely used in mining and oil exploration owing to their ability to withstand extreme conditions. Their cutting efficiency and durability reduce drilling time and costs.
Diamond core drills are used in rock core sampling and geological surveys. These drills allow for precise drilling with less heat and wear.
Polycrystalline diamond compact drill bits find usage in oil, gas, and mineral drilling. They significantly improve drilling speeds as well as extend tool lifespan compared to traditional carbide bits.
Synthetic diamond-tipped core drills are used for boring through concrete, marble, and other materials. They have become key tools in bridge and tunnel construction.
- Synthetic Diamond for Grinding and Polishing
Synthetic diamonds also play a key role in grinding and polishing processes. They are widely used across automotive, aerospace, electronics, and tool-making industries for precision grinding.
Synthetic diamond grinding wheels are being employed to polish metals and sharpen carbide tools. Similarly, nano-diamond abrasives are utilized in ultra-precision polishing of semiconductors and optical lenses.
Advancements in material science and nanotechnology are making synthetic diamonds more sophisticated. As a result, the application areas are expanding rapidly. They are gradually replacing natural diamonds in industrial applications like cutting and drilling due to their cost-effectiveness, controlled properties, sustainability, and easy availability. These lab-grown diamonds provide unmatched efficiency and durability.